With the increasing popularity of PE pipes, they are now being utilized in various fields such as oil and gas, water supply, drainage, and electrical engineering. Ensuring construction quality, purchasing high-quality PE pipes, mastering the use of PE pipe hot melt welding machines in construction, and becoming proficient in the construction process are all crucial for ensuring the quality of engineering construction.
PE pipelines themselves possess characteristics such as corrosion resistance, zero pollution, long service life, easy installation, and faster speed. There are mainly two ways to connect PE pipelines: electrofusion and butt welding. Currently, the preferred method chosen by supervisors is hot melt welding.
The principle of hot melt welding is to bring two PE pipes into close contact with each other and heat them evenly using a special electric heating tool until they melt at their interfaces. Pressure is then applied to maintain the connection until the joint cools, forming a single integrated unit. Here is a detailed explanation of the specific operation method.
Preparation for butt Fusion Connection. The tasks for preparing for fusion connection installation are as follows:
- Load the couplings with the same specifications as the pipe into the machine rack.
- Prepare sufficient supports in advance to ensure that the pipeline to be hot melt connected is at the same height as the centerline of the machine rack and can be easily moved.
- Set the temperature of the electric heating plate to 200-230°C, typically around 210°C.
- Connect the main power supply of the hot melt welding machine, turn on the power switches for the electric heating plate, cutting tool, and power oil pump, and perform a trial run.
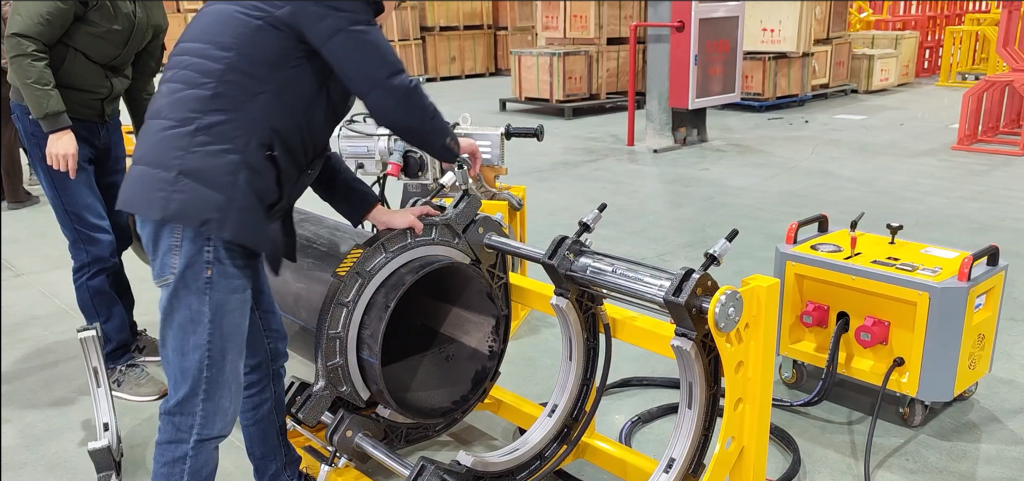
Butt Fusion Connection. The processing procedure for hot melt fusion connection is as follows:
- Verify whether the specifications and extrusion pressure of the pipes to be hot melt fused are appropriate, and check if there are any dents, bumps, or scratches on their surfaces. If the depth of scratches exceeds 10% of the pipe wall thickness, partial removal should be carried out before application.
- Clean the oil and debris from both ends of the pipes with soft paper or cloth dipped in ethanol.
- Place the pipes to be hot melt fused into the couplings on the machine rack, ensuring that the lengths extending from both ends are equivalent (as short as possible without affecting milling and electric heating, ideally maintaining 20~30mm). Support the parts of the pipes outside the machine rack with supporting materials to ensure that the axis of the pipes is at the same height as the centerline of the machine rack. Then secure them with the couplings.
- Insert the cutting tool, turn on the power switch of the cutting tool, then bring the ends of the pipes together and apply moderate extrusion pressure until continuous chips appear at both ends (chip thickness should be 0.5~10mm, adjustable by adjusting the height of the milling cutter). Release the extrusion pressure, wait for a moment, then retract the movable frame and turn off the power of the cutting tool.
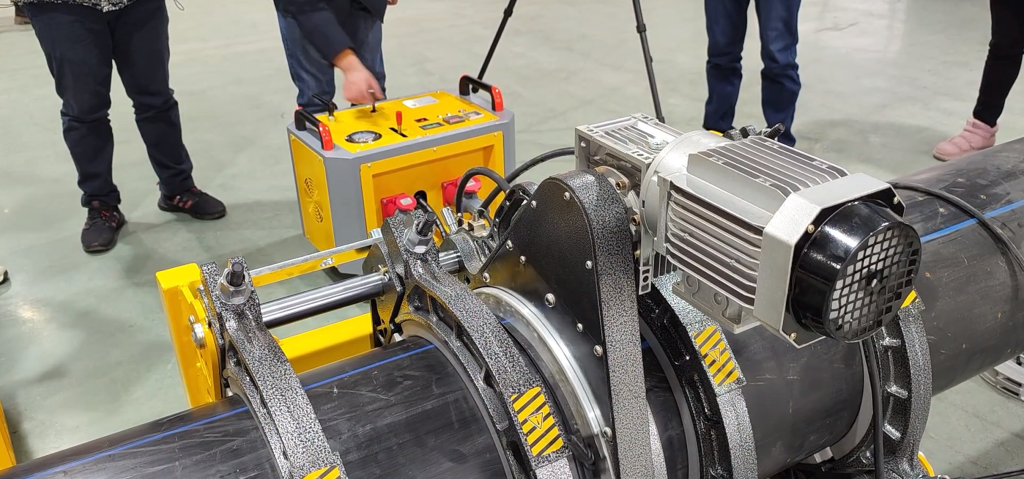
5.Remove the cutting tool, bring the two pipe ends together, and check for alignment (the misalignment of the two ends of the pipeline should not exceed 10% of the wall thickness, which can be improved by adjusting the straightness of the pipeline and the tightness of the couplings; the gap between the ends of the pipeline should not exceed 0.3mm (below de225mm), 0.5mm (de225mm~400mm), 1mm (above de400mm), if not met, milling should be done until requirements are met).
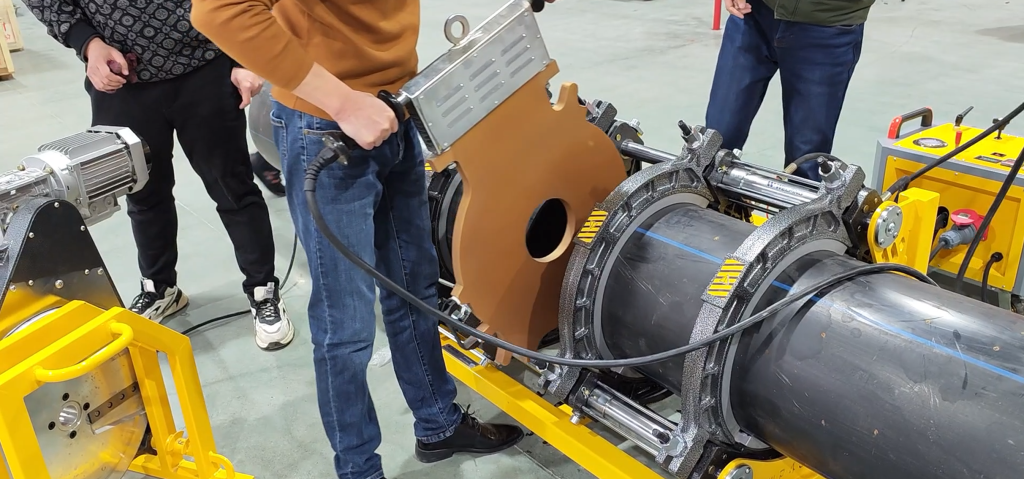
6.Once the temperature of the electric heating plate reaches the set value, place it into the machine rack, apply the required extrusion pressure until the minimum curling height on both sides is achieved, then reduce the extrusion pressure to the standard value (with the ends of the pipe touching the middle of the electric heating plate, facilitating heat absorption). After a specified duration, release the movable frame, quickly remove the electric heating plate, then bring the two pipe ends together. Minimize the transition time, and after cooling for the required duration, release the pressure, loosen the couplings, and remove the connected pipeline.
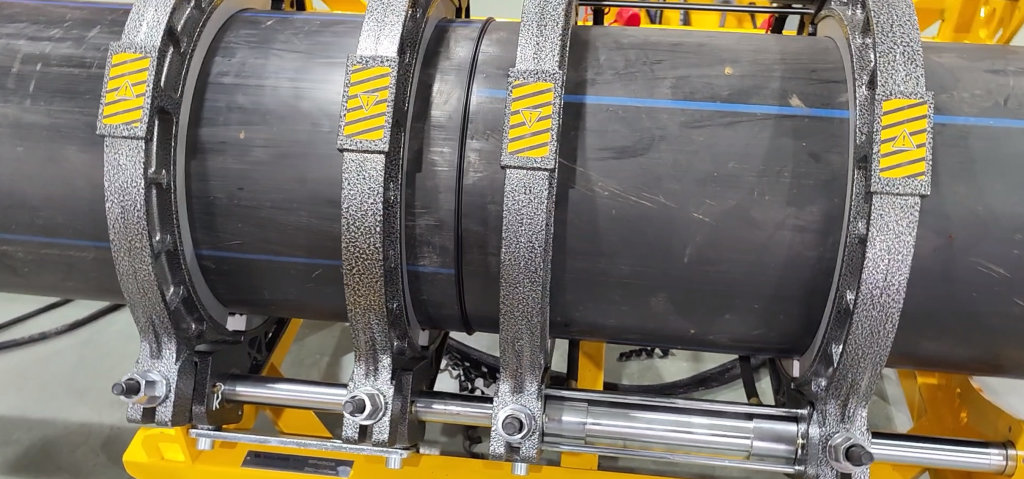